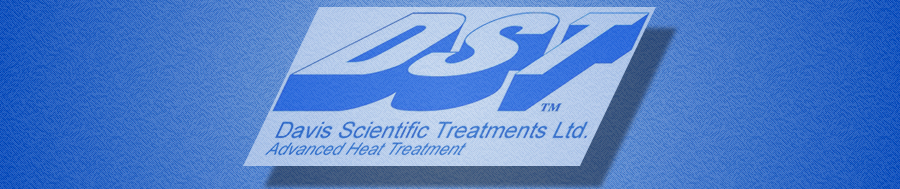
Vacuum Brazing of Titanium
Introduction
Davis Scientific Treatments has been carrying out the vacuum brazing of titanium, in many special applications. We have developed equipment to overcome the substantial difficulties to be found in perfecting joints.
The brazing of Titanium alloys has been well researched for many years. It is widely used where the high strength to weight ratio is important, for example in aerospace applications, both aircraft and space vehicles. The excellent corrosion resistance of Titanium is an important factor in it's widespread engineering usage.
High fatigue strength, and fracture resistance, make Titanium alloys attractive in chemical and petroleum industries, as well as in automotive applications.
Titanium and it's alloys are often used in manufacture of heat exchangers, tanks, reactor vessels, and other chemical devices.
Jointing Titanium with other Materials
The major problem with Titanium is the difficulty, and high cost, of jointing with other materials.
Titanium will form brittle compounds with most other metals, if directly they are jointed by fusion welding, for example. Most common structural materials, which includes aluminium and ferrous alloys, are not compatible with fusion welding.
However, Titanium can be brazed to most steels, refractory metals, copper and aluminium, nickel alloys, ceramics, and polymer composites.
Brazing Alloys
Generally, there are a number of active braze alloys, which have been developed over a number of years; these improve strength, and corrosion resistance:
- silver based
- titanium based
- aluminium based
- zirconium based
- palladium based
The latter have been found to work well with high temperature applications.
A technique commonly used to enhance joint wetting characteristics is the use of a thin nickel layer deposited by the PVD process, to serve as the brazing filler metal. The shear strength of the joints is improved.
Complex configurations and geometry can be accommodated, provided that it is possible to abut the jointing faces closely and accurately.
Brazing is beneficial, because it involves melting of the filler material only. This process therefore acts to eliminate the problems occurring in the jointing of dissimilar metals with fusing operations.
Moreover, on account of the lower temperatures involved, distortion of assemblies is minimised.
Advantages of Vacuum Brazing
Brazing does not melt the base metal of the joint. However, Titanium has to be processed in a manner, where the base metal is protected from oxidation. Hence, the use of brazing in a vacuum meets this requirement.
Vacuum brazing is attractive, as it produces higher quality joints than any other known brazing technique. The process is non-polluting, as the brazed surface is free of any contaminants, considered corrosive to titanium.
Reliably repeatable results are gained from vacuum brazing. Our furnaces are designed and manufactured to achieve accurate vacuum level and temperature conditions, necessary for every process batch.
Davis Scientific Treatments (DST)
Here at DST, we have specialised in development of brazing of titanium, to a number of metals, and to ceramic based materials.
We have been very active in the conducting of R & D trials, to promote successful brazing of titanium, to a range of materials, using a number of commercially available alloys.
DST has much R & D experience in this field, gained from many applications. We have vacuum furnace equipment, which is dedicated to testing any customised titanium brazing application, so as to find an effective process solution.