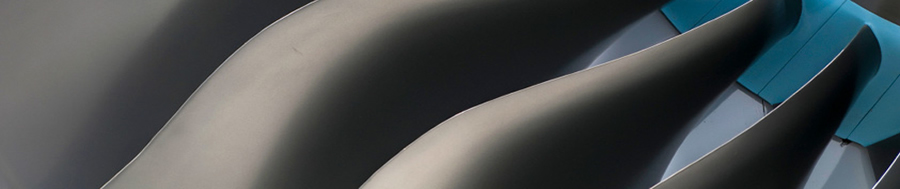
Hydrogen Embrittlement
Introduction
Sudden brittle fracture in high strength metal alloys is a very serious issue in industry, especially as it often arises from the effect of factors that have occurred during manufacture.
This phenomenon, known as Hydrogen Embrittlement [HE], reduces ductility, commonly to the level of ceramics, resulting in lowering of fatigue strength, and fracture toughness.
Brittle fracture occurs without warning, sometimes just after manufacturing processes.
It is known as the "Achilles Heel" of high strength alloys.
Susceptibility of Metals
HE is found in a wide variety of metals. These include steels, and aluminium at high temperatures, and titanium. Some irons are susceptible.
Other metals include nickel alloys, copper (including beryllium copper), vanadium, tantalum, zirconium, palladium and cobalt. Stainless steels are less susceptible to HE.
As the strength of a steel alloy increases, so does the risk of loss of fracture toughness is encountered.
Effect of Temperature
Hydrogen is normally only able to enter the metal structure as atoms or ions, enabled by the small size. Thus, gaseous hydrogen is not absorbed by metals at ambient temperatures. In a gas, the hydrogen in the normal molecular form, consists of pairs of atoms tightly bonded together.
As the gas temperature rises, the molecules are more enabled to split into the constituent atoms. This process allows the possible absorption into metals.
As higher temperatures are found in many production processes, hydrogen absorption takes place in casting or welding, for example.
The absorption of hydrogen ions occurs in chemical reactions, for example, electro plating, cathodic protection, and indeed in corrosive environments.
Process of Hydrogen Embrittlement
HE is a complex process, involving a number of distinct contributing mechanisms.
During fabrication or melting processes, as well as in service, hydrogen can come into contact with metals, and is absorbed. It is known that the atoms are first of all able to penetrate the metal surface, where it can diffuse in ionic form.
Once inside the crystal lattice, the hydrogen can react, irreversibly, with oxides or carbides, to produce permanent damage. This is especially true with titanium and vanadium.
By interacting with lattice dislocations, grain boundaries, or voids, the hydrogen atoms produce a brittle structure.
The atoms can recombine at crystal defects to form gaseous hydrogen. At the outer surface, this action causes blisters. In some metals, hydrides are produced, reducing the mechanical properties, which again is common with titanium and vanadium, but less so in steels.
Some types of embrittlement are reversible, often where no other chemical reaction has occurred within the lattice. If cracking has not taken place, and environmental conditions prevent hydrogen generation on the metal surface, it can diffuse out of the material, restoring ductility.
Prevention of Hydrogen Embrittlement
Material selection is very important in consideration of HE control. Most vulnerable metals are high strength steels, titanium and vanadium alloys.
Other materials are less susceptible, including stainless steels, copper, some nickel alloys, and aluminium at lower temperatures.
Most mitigation measures involve minimising contact between metal and hydrogen. Special care must be taken with all plating processes, for example chromium and zinc. This applies also to electroless nickel plating, and acid pickling. With welding, use of dry rods is essential.
If the metal has not started to crack, there is a process called Low Hydrogen Annealing, or "baking", where the material is held at high temperature for many hours, in a vacuum. This procedure allows hydrogen trapped, within the metal, into diffuse out.
Davis Scientific Treatments has facilities to carry out this process. Please contact us in case of any query, or application, if you need a quotation, or any advice. We are always very pleased to assist.