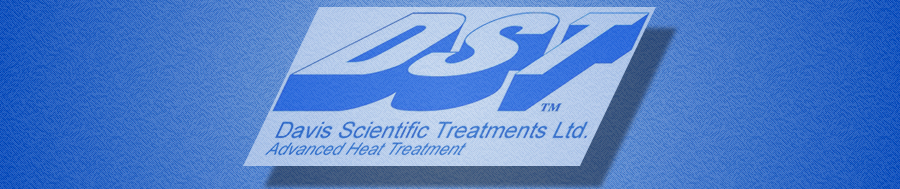
Additional Features & Benefits
Process of Electron Beam Welding
At the position of the focussed electron beam, the kinetic energy heats the workpiece material above the melting point. The energy of the electrons vaporises the material.
The size of this focal spot can be smaller than 80-90 micrometres. Hence there is created a weld pool, of molten material, which is surrounded by a melting mantle.
The weld pool can be considered as a conical slot, tapering from the workpiece surface into the material. As the electron beam moves on it's programmed path, this conical slot of molten material progresses.
At the front of the slot, material is being melted, which then floats around the conical profile. At the rear of the beam path, the molten material is solidifying, forming the joint.
Beam Welding Features & Benefits
- There is a wide range of materials, including difficult to weld materials.
Chemically active metals, such as beryllium, titanium and zirconium
can be welded.
Refractory metals can be welded, including molybdenum, niobium and tungsten. Even copper can be processed. - Electron beam welding is a fast process. Because the heating is locally concentrated into a small area, distortion of workpieces is minimal. The beam energy heats components within milliseconds, and so enables narrow welds, with small affected zonal heating.
- The process uses a high vacuum in the welding chamber. Molten material is degassed, thereby reducing impurities in the heated area. No additional means of oxidation prevention is needed, e.g. use of inert gases. The resulting weld is clean, with no oxidation.
- It is good for delicate assemblies, as the electron beam is very localised, and allows surrounding material to stay cool. Heat sensitive products, e.g. populated electronics enclosures, can be processed.
- Fully automated beam welders provide very precisely located jointing of workpieces. It gives extremely good repeatability and traceability of the welding parameters. Documentation of the process is such that it is used extensively in critically traceable industries, for example, in aerospace applications.
- Because the material of the workpieces, only, is melted, to create the joint, no filler materials are used.
- In electron beam welding, unlike MIG, TIG, and arc welding, the process is performed with only a single motion around the joint. Therefore, it is a cost effective process.