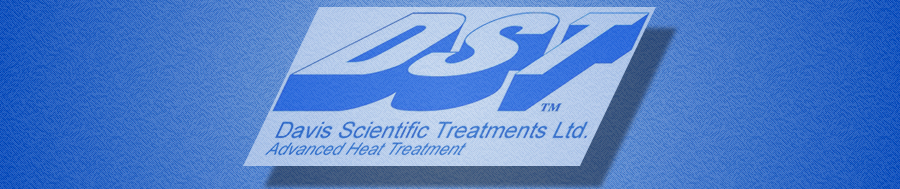
Other Standard Heat Treatments
At Davis Scientific Treatments, we offer the following heat treatments, with a fast turn around time usually, to help our customers with their planning of their production processes.
With many of these heat treatments, the process fully conforms to the NADCAP Certification protocols. Please contact us to check which Certifications apply to any particular treatment.
Case Hardening/Carburising
Carburising, also referred to as Case or Cyanide hardening, is a process whereby the work piece surface is produced which is then resistant to wear, but maintains the strength and durability and ductility of the core. Fatigue endurance is also enhanced.
This treatment is applied to low Carbon steels, after rough machining, as well as certain high alloy parts.
In carburising, the material surface is exposed to a gas or a liquid rich in Carbon. The carbon diffuses into the steel, which produces a surface layer up to 1 mm thick.
In liquid carburising, the components are placed in a molten salt bath, often containing about 25 % sodium cyanide. The case depth obtained is proportional to the time exposed in the Carbon rich environment.
Nitriding
Gas nitriding is a surface hardening process. Using ammonia gas, nitrogen is added to the surface of parts, usually steel.
It develops a very hard surface, but only with a thin surface case.
It takes place at low temperature, and quenching is not needed.
A wide range of steels can be processed, including tool steels, where wear resistance, improved fatigue properties, and minimum dimensional changes are required.
Nitrocarburising
The addition of the element Carbon, usually from a suitable gas, provides a thicker hardened surface from that gained with Nitride process. Sometimes Nitrogen and Oxygen are arranged to diffuse into the surfaces.
Use of hydrocarbon gases is a safer and cleaner method, than for example cyanide salts, used in carburising.
Greater corrosion resistance often results. It has the ability to harden materials which are not pre-hardened. Distortion is minimised, and fatigue strength is improved.
It is a relatively low cost process, compared with carburising. It is commonly applied to low alloy steels, mild steels and cast irons. Any stable steel at the process temperature can benefit from this treatment.
Tufftriding
Tufftriding is a low temperature surface hardening process. The components are treated in a heated salt bath. A chemical reaction occurs, where Nitrogen and Carbon are absorbed into the surface of the parts.
Tufftriding is similar to Nitriding, but results in a much more ductile layer, and is applicable to a wide range of steels and cast irons.
The layer reduces wear, and also lowers the coefficient of friction. Tufftriding is a low distortion process.
Chemical Blacking
The components are treated in a hot bath, containing oxidising salts, often of a high alkaline nature, where a chemical reaction produces a black oxide coating. Often the process is also called Blackodising. For certain applications, the salt bath may be cold.
It is usually applied to ferrous materials, but not stainless. Carbon steels, unalloyed and alloy steels can be treated.
Unlike other finishes, no dimensional alteration is obtained, which is of great benefit, where parts with high tolerances are being processed.
Black oxide coatings offer small increase in resistance to corrosion, and improved lubricity is also obtained.
Tool Steels
Here at Davis Scientific Treatments we offer a full range of heat treatments for all types of tool steels.
All treatments consist of the same 4 basic steps:
- Pre-heating: heating rapidly to temperatures where atomic structure begins the change to austenite
- Heating (Austenitisation): transformation at temperature where the ferrite structure changes to austenite
- Quenching: rapid cooling of the hot austenite to the much harder desired end state martensite micro atomic structure
- Tempering: tempering tool steel makes the newly formed martensite less brittle. It is an essential step in the process.
Induction Hardening
Induction hardening offers significant advantages for heat treating alloy steels. The process is particularly suitable for metals with Carbon content exceeding 0.3 %, notably hardened steel with low alloy content.
The process involves generation of heat directly into the work piece. The main advantage is that the material is quickly taken to the desired hardening temperature. This is achieved using high frequency electromagnetic fields, transmitted via coils surrounding the work pieces, usually made from Copper.
The material is then quenched as normal, in order to develop the martensite phase micro structure. Low temperature tempering operation achieves the desired blend of hardness and toughness.
CAPACITY LIST -- COMMERCIAL
Aluminium Heat Treatment: | Controlled drop bottom furnace into cold and hot water 2400 mm L + 1200 mm H + 1200 mm W |
Vacuum Heat Treatment: | 2000 mm L + 1200 mm H + 1400 mm W |
Stress Relieve: | 2800 mm L + 1200 mm H + 1400 mm W |
Temper (Air): | 2000 mm L + 1200 mm H + 1200 mm W |
Harden + Temper Seal Quench | 1200 mm L + 600 mm H + 720 mm W |
Salt Bath: | 900 mm H + 550 mm H + 500 mm H |
Tufftride: | Call to confirm |
Cold Chemical Black: | 600 mm L + 460 mm H + 350 mm W |
Gas Nitride: | 1500 mm Dia + 1500 mm H |