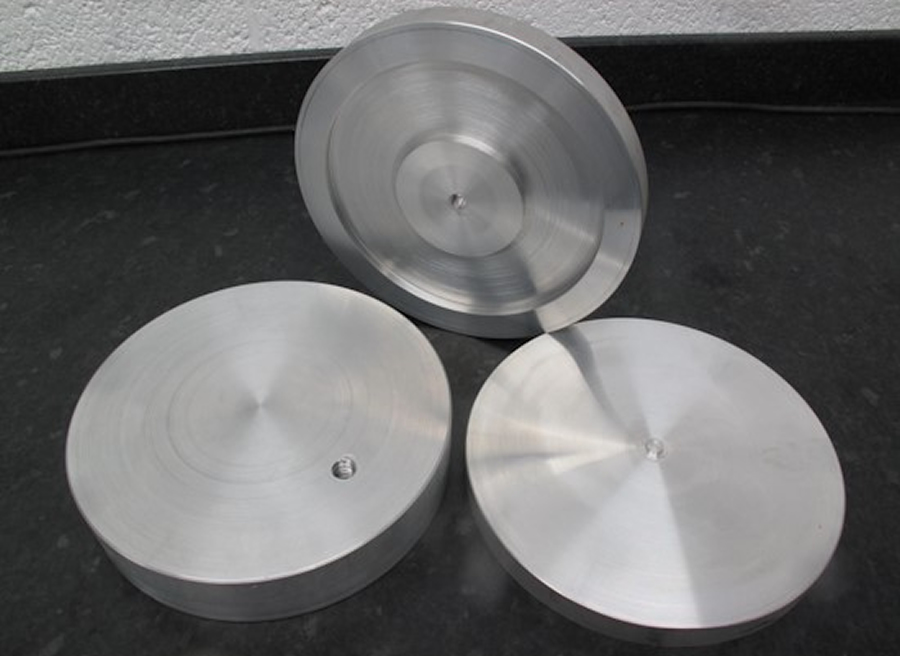
Vacuum Brazing of Aluminium - Research and Development Progress
Conventional Aluminium Brazing
As is well known, brazing of aluminium components is historically a very difficult process, the reasons for which are given elsewhere here.
Conventionally, it has been carried out using the 'salt bath' process, sometimes referred to as 'dip' brazing. The components to be brazed are 'wetted' by the filler metal, to achieve the bond. This is performed by immersion of the assembly in a bath of molten salt flux. The process removes the oxide on the aluminium, and melts the brazing alloy, to form a strong joint.
However, there are many disadvantages:
- Dimensional accuracy is hard to achieve, and distortion is common.
- Considerable post-braze cleaning is required, with much braze surplus.
- Close attention needed at design stage to avoid air traps, weakens joint.
- Large impact on the environment.
- Production of corrosive vapours, and large quantity of waste water.
- Expensive process to carry out, when compared with vacuum brazing.
For these reasons, the salt bath process is decreasingly used.
Davis Scientific Treatments Ltd [DST]
After extensive R & D effort, extending over many years, DST has developed and perfected new methods for brazing aluminium.
The techniques we employ have overcome all the disadvantages, listed above, of the 'salt bath' process.
This field is becoming very important, as new manufacturing operations call for the accurate joining of aluminium parts. Typical applications include heat exchangers, electronic assemblies, and many in aerospace.
We can now offer a service to accurately braze together components in aluminium, using a range of material specifications. The parameters we have worked on successfully include:
- Best form of braze material, e.g. foil shim thickness, or paste formula.
- Accuracy of vacuum, to minimise surplus braze material.
- Development of techniques for different cross-sections and shapes.
- Production of clean, and 'as machined', cosmetic finish.
Our extensive R & D trials have been conducted, using a range of different parameters, to optimise the vacuum process:
- brazing temperature
- vacuum levels
- soak time at temperature
- heating cycle rates
- cooling cycle rates
- methods to minimise oxidation
- shim thickness and material
- paste formula and amount
Please contact us for an in-depth analysis of your particular aluminium brazing application. We can then supply our proposal for your consideration.
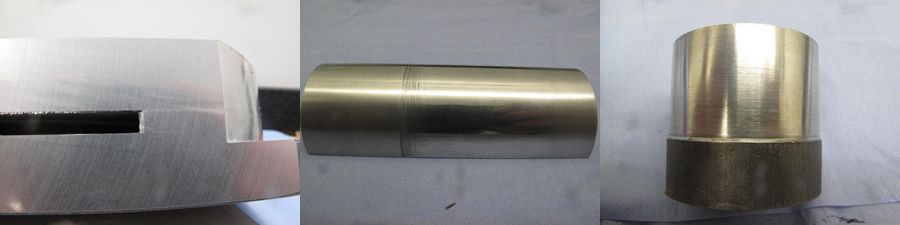