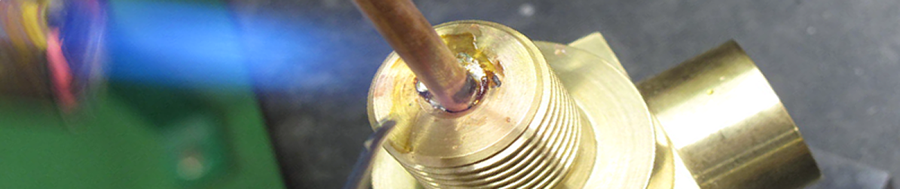
Torch Brazing Operations
Introduction
Brazing using a torch or flame is a process which can be used to join similar or dissimilar metals or alloys. Base metals which can be torch brazed include steels, copper, brass, aluminium and stainless steels.
A quality joint is obtained when the process is carried out correctly, in spite of a popular belief that brazing is an inferior substitute for welding.
For example, brazing brass has a strength and hardness near that of mild steel, and is much more corrosion resistant.
Generally, torch brazing yields the following benefits:
- ductility
- strength
- leak tightness
- ability to withstand pressure and vibration changes
- corrosion resistance
- appearance [smooth and clean]
Silver brazed parts can be machined precisely, after joining.
Davis Scientific Treatments [DST] carries out many torch brazing applications, found in a wide range of industries.
Advantages
Brazing has many advantages over other metal-joining techniques:
- Brazing does not melt the base metals in the joint.
- It allows much tighter control over tolerances, and produces a clean joint, without the need for further finishing.
- Non similar metals, and non metals [e.g. metallised ceramics] can be brazed together.
- The lower temperatures of brazing are less likely to distort the work pieces, or significantly change the crystalline structure.
- Complex and multi-part assemblies can be brazed cost effectively, including thin work pieces. Brazing is less likely to result in burn-through.
- Brazing is easily adapted to mass production. The individual process parameters involved are less prone to variation, so lend themselves to automation of processes.
Disadvantages.
The lack of joint strength has to be taken into account, due to the softer filler materials used. The strength of base metals is usually greater than the filler metal.
Brazed joints can be damaged under high service temperatures, so are usually limted in service by this factor.
Brazing Process
In the metal joining process, the filler alloy [commonly called solder] does melt, but there is no melting of the component parts of the assembly.
Rather, the solder on melting flows into the joint between the parts, drawn by capillary action.
The base metals are not fused, but the filler diffuses into the metal, making a surface-only alloy with the components.
The joint clearances are small, to optimise the capillary action of flow.
A properly designed soldered joint can turn out imperfectly, unless the correct procedures are carefully followed. These are descrbed in 6 basic steps.
Torch Brazing Steps.
1. Good fit and proper clearances.
As has been noted, torch brazing relies on capillary action to flow the molten filler between the base metal surfaces.
Therefore, during the brazing operation, the clearance between base metal components has to be carefully controlled, and maintained unaltered.
2. Cleaning.
Any contaminants on the joint metal surfaces will inhibit proper brazing, as they will form a surface barrier.
All oil or grease, or other dirt, must first be removed with a degreasing solvent. Sometimes a chemical treatment is required, e.g. acid pickling.
3. Fusing the components.
Flux is a chemical compound which is applied to the surfaces of the joint, prior to brazing. When the metals are heated, oxides are formed, which action must be minimised. These inhibit the filler metal from wetting, and bonding to joint surfaces.
Flux should be applied liberally to the base metals, preferably just prior to, or during, brazing if possible.
4. Assembly of the joint.
The parts have to be positioned so that they do not move during brazing. They have to be held in correct alignment throughout the process.
The easiest way is to use gravity, if shape of joint permits. Sometimes a clamping device is required.
If necessary, a jig can be made. It should be designed for minimum contact with the components, to reduce heat conduction from the joint. Often jigs are used in bulk production applications.
5. Brazing operation.
The actual brazing operation involves heating the assembly to soldering temperature. Usually a hand held torch is used, fuelled by gas [often acetylene].
With some common solders, the point at which the flux becomes clear does indicate that the joint area is at or near temperature.
In heating pieces of unequal mass, the torch should be applied to the heavier item. In joining 2 different metals, the one with greater thermal conductivity should be favoured.
6. Cleaning the new joint.
Firstly, the residue flux is removed, for which there are various methods, including use of water based solvents.
Secondly, the assembly may be pickled in an acid, to remove any oxide scale, formed during the operation.
We have discovered recently that, after cleaning, immersion of the parts in a specific acid solution, greatly improves the quality of the subsequently brazed joint.
Davis Scientific Treatments [DST]
DST has extensive experience in the field of torch brazing, using both similar and dissimilar metals.
We are always pleased to advise on a customer's particular requirements, for which we invite details of any application.
Please contact us for an in-depth analysis of your particular torch brazing application. We can then supply our proposal for your consideration.