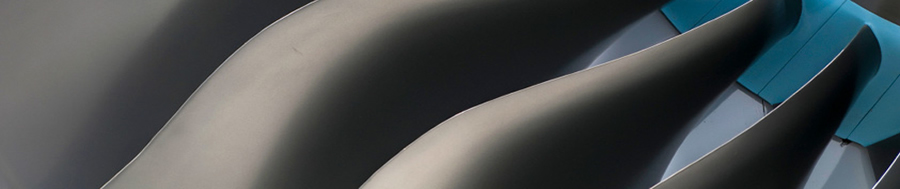
Ceramic to Metals Brazing
Introduction
The use of ceramics in engineering has become very important in recent years.
Ceramic materials possess a wide range of thermal, mechanical and electrical properties. Alumina has low thermal conduction, whereas diamond has high thermal conduction. Ceramics are used as low weight electrical insulators, and are found in superconducting electrical assemblies.
This paper is an update on research Davis Scientific Treatments has been carrying out in recent years.
Metals to Ceramics Applications
Ceramics are hard, but brittle in nature. They are lightweight, and stable at high temperatures. They have low fracture toughness.
Most metals are ductile, soft, and have better fracture toughness. They have often less strength.
There are many applications where this combination of properties involves use of metal-ceramic assemblies.
Typical applications include:
- Medical implants
- Mass spectometry
- Gas detectors
- Aero engines
- Gas lasers
- Nuclear detectors
- Opto electronic sensors
- Rechargeable batteries
- Micro electronic packaging
- Metal-ceramic seals
- Power engineering
- Cryogenic applications
- Measurement devices
- High vacuum technology
As may be seen, there is a vast array of modern technological applications, for jointing of metals to ceramics.
Ceramics to Metals Bonding
To obtain a high integrity joint between a metal and a ceramic material is a challenge. The very properties of ceramics, that make them attractive in engineering products, pose major handicaps for joints processing.
Due to the chemical inertness of ceramics, conventional joining methods cannot be used. It is extremely difficult to achieve 'wetting' of the joint surfaces. In active metal brazing, a metal [often Titanium] is added to the braze alloy to promote a reaction, which then causes a product, which can then form the joint, with the braze alloy.
This reaction takes place with the active element, within the filler metal, for example Titanium, to produce oxides, carbides, or nitrides. This process allows the filler metal to wet the surface of the ceramic.
Ceramic to Metal Brazing Factors
As explained above, Titanium is the most commonly used element used in the production of the required active brazes. Other elements that are employed include Hafnium, Chromium, Vanadium and Zirconium.
The exact composition of the intermediate layer formed during brazing is affected by:
- concentrations of the active elements
- temperature characteristics of the cycle
- vacuum parameters if used
The materials will have significant differences in thermal expansion coefficients. Care has to be taken during cooling, to avoid cracking of the ceramic component. This means that joint design is a critical part of a successful product design. Moreover, the rate of cooling after the brazing operation is clearly a critical part of the process.
The reactivity of active metal brazes generally does require the brazing operation to be performed in a vacuum, or in an inert atmosphere. This process protects the base materials, and the filler metals, from atmospheric contaminants, both Oxygen and Nitrogen.
The vacuum level is quite high, for these reasons. A major advantage of a vacuum braze operation is that the resulting parts are extremely clean, and ready for immediate use.
Davis Scientific Treatments [DST]
For many years now, DST has been pioneering the research into active metal braze compositions. We have experimented on many shapes of assembly, using different ceramics, such as carbides, nitrides, oxides, alumina, sapphire, and diamond.
We have produced joints with metals such as Copper, Aluminium, Titanium and Stainless Steel.
The research has included work on joint design improvements, and on the optimum heating/cooling cycle parameters, for each joint combination. As highlighted above, the differing thermal expansion rates is an important factor in the consideration of joint design.
These developments take up much time, and because there are so many different materials to be joined, the nature of the work continues from year to year.