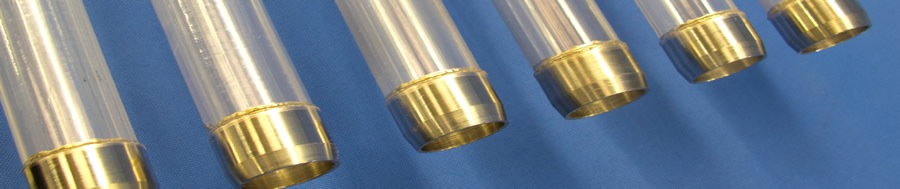
Vacuum Brazing of Ceramics
Introduction
Davis Scientific Treatments has been developing the vacuum brazing of ceramic components, in many special applications. We have identified particular processes, to overcome the many known difficulties involved in the forming of ceramic joints.
It is well known and widely recognised that the properties of ceramics are increasingly found as a vital constituent in a wide range of modern engineering applications.
These properties include: desirable electrical characteristics, high mechanical strength, good thermal conductivity, and high hardness.
These properties are very valuable at high temperatures, due to the excellent thermal stability of ceramics.
Applications of ceramics.
New applications are continually being innovated. Sensors, electronic packaging and power electronics need solutions, for thermal management,electrically conductive joints, and hermetic seals.
Sensor windows of quartz or sapphire require joining to metal housings. Aluminium oxide and aluminium nitride are used as insulating bases, where high voltages have to be isolated.
Another important use of ruby and sapphire materials is in orifice type applications: these include high pressure water jets, flow meters, control valves, and ink jet systems.
Here, it is the chemical inertness, and extreme wear resistance to heat and abrasion, of the ceramic which is employed.
They are also very valuable in low speed oscillation applications, where excellent low torque, and low break-away friction, is important.
The ruby or sapphire orifice components usually must be mounted in a metal housing, where the need for a sound brazed joint is paramount.
Difficulties with ceramic brazing.
Because of the high temperature uses of ceramics, braze alloys in the jointing process often must have higher temperature capability, than most that are currently available.
The 'active' brazing alloy has to be capable of 'wetting' the ceramic surface being jointed, which is usually extremely difficult.
Solution of this severe problem makes it possible to effect the direct brazing of ceramic to itself, other ceramics, and a whole range of metals.
With metals, the respective thermal coefficients of expansion, between mating parts, is of paramount importance. Stresses during the cooling phase, in particular, must be minimised.
Operational considerations in ceramic brazing.
The filler materials are formulated to incorporate an 'activating' element.Often this is Titanium based, but other elements are sometimes used, for example Hafnium and Zirconium.
During the brazing process, which must be carried out under high vacuum, sometimes dry hydrogen or argon, the activating element reacts with the ceramic to form complex metallurgical phases, that wet the molten filler material.
Ideally these alloys will retain their strength and ductility, at temperature, as well as having good oxidation resistance. Even graphite has been joined, for use in excess of 2700 deg C.
When brazing ceramics, careful consideration must be given to the design of the joint. On cooling, the braze alloy [and metal component] will contract more than the ceramic component.
This will introduce residual stresses into the joint. As ceramics perform better in compression, the joint should be designed, where possible, to keep the ceramic component in compression.
Davis Scientific Treatments (DST)
At Davis Scientific Treatments, we have considerable development experience of brazing ceramics to metals with similar thermal coefficients, e.g. Invar and Kovar, which have rates close to silicon carbide and silicon nitride.
The photograph shows sucessful brazing of sapphire tubes to Kovar end pieces.
Other ceramics that can be brazed are: alumina, zirconia, glass, boron carbide and aluminium nitride.
We are always ready and willing to give our advice, or share our expertise, at the design or prototype stage, on physical or metallurgical characteristics.
We are keen to pioneer any new ceramic brazing application.