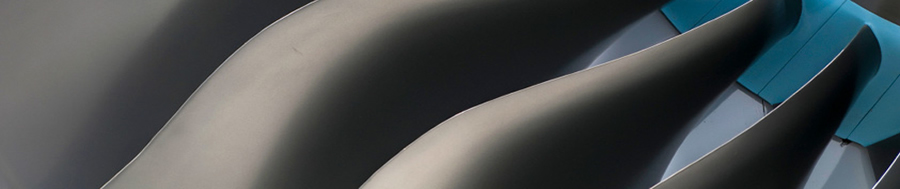
Further Considerations in Vacuum Brazing of Aluminium
In industrial processes, a heat transfer exchanges the heat generated by a device, away from the device to a fluid medium, such as air, or a liquid coolant.
This process is commonly used in many household and industrial devices, where excess heat has to be dissipated, to maintain device performance. The process product is known as a heat sink, or heat exchanger. Many current applications of devices now involve such heat exchangers.
The vehicle market is forecast to become the largest market for use of Aluminium and its alloys. Specific transport applications include electric vehicle battery housings, replacing more expensive and heavier Copper. Other uses involve air conditioners, HVAC and refrigeration, and of course many in aerospace industries nowadays.
The most common materials used are Aluminium and Copper, as both metals are very good conductors of heat. However, Aluminium has light weight, corrosion resistance, and low cost: these factors make it an increasingly desirable material for such products described. In particular, it can be shaped into foil, sheets or fins, making it ideal for heat transfer applications.
The brazing of aluminium components and assemblies is a metal jointing technique, where a filler metal alloy is heated above its melting temperature, but below the melting point of the metals being joined.
The liquid filler alloy, at the soak temperature, is drawn into the gap, between the closely fitting surfaces at the joint interface, by capillary action. Because of the importance of surface "wetting", and capillary effects, the quality and cleanliness of the joint mating surfaces is critical. Furthermore, careful control of joint clearance is essential, as it has to be minimised.
Brazing, when performed correctly, produces excellent joints, especially when fixing thin-walled, compact assemblies. Aluminium and its alloys require extremely careful control, especially since the brazing temperature is very close to the melting point of aluminium.
Many of the problems associated with Aluminium brazing are related to the complexity of the temperature rise and cooling profile. Manufacturers do not want premature melting of the brazing alloy, or localised areas of heat, creating "hot spots". Heating has to be made evenly across the base metals.
Another difficulty occurs when brazing Aluminium to other metals. Owing to differences in thermal expansion rates, stresses are set up in the area of the joint, during heating, and subsequent cooling.
Because Aluminium readily forms a tough oxide film, during brazing, means must be found to scavenge all Oxygen atoms during the process. Obviously, brazing in a high vacuum furnace is very desirable, for this reason.
If not done correctly, the high brazing temperature, relative to melting point, significantly lowers the strength of the base Al alloy. The potential softening effects must be considered when alloy and filler material are chosen.
DST has carried out extensive R & D work in Al brazing, over many years. We use vacuum furnaces for all research. This method of operation eliminates most of the risk of oxidation and contamination. This risk can occur when the braze filler melts, and flows into the clearance gaps between mating parts.
Vacuum brazing is a high-end jointing technology. It results in assemblies of extremely strong joints. Successful vacuum brazing requires a short process cycle -- that is, a fast pumping and heating furnace cycle. Good temperature uniformity, around the furnace chamber, must be obtained at soak temperatures.
Hence, vacuum furnace design and manufacture is a critical aspect in the achievement of successful Al joints. With such furnaces, the vacuum brazing operation is highly repeatable, necessary for volume production.
Our experience with furnaces has led us to the necessity of designing and building our own bespoke furnaces.
From the details above, it is clear that there are many aspects to the Aluminium brazing process. The successful parameters can only be determined effectively by continuous development of operational characteristics.
This is the nature of the R and D work at DST.
DST is aiming to overcome the previously described difficulties in obtaining strong joints between aluminium alloy components, and other metals. DST is using a specially constructed furnace, for this purpose, employing high vacuum.
Below are listed the technical steps which have to be considered, and which must be processed for each brazing operation.
The complete procedure for each brazing trial is an empirical process of experiment. Accurate and systematic amalysis of the results, leads to the judgement of success or failure, of the particular criteria used in the test.
- design and manufacture of high performance vacuum furnace
- types of aluminium alloy, and other metals, being brazed
- methods of obtaining sufficient cleanliness of parts
- types of appropriate braze filler materials
- use of "cladding" on aluminium sheets
- choice of filler paste or foil for brazing
- design and manufacture of 'fixturing':
- necessary to present parts into a stable sub-assembly, with close joint separation, ready for brazing
- obtaining the successful temperature profile in the furnace:
- heating temperature rise
- settling profile at braze soak temperature
- dwell time at soak temperature
- cooling temperature fall
- use of Oxygen reduction methods, e.g. magnesium pellets, type and amount
- annealing after brazing operation
- inspection of final joint, to assess strength and uniformity
- sectioning of joint, and hardness testing