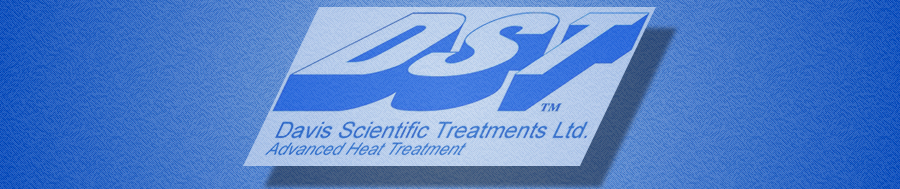
Electron Beam Welding
Introduction
Davis Scientific Treatments has taken advantage of considerable knowledge, within the Company, to expand its offered services.
We have purchaed an Electron Beam Welder machine (EBW). This is capable of weld jointing small components, having a vacuum chamber of a 300 mm cube.
This new facility augments our existing heat treatment and braze jointing processes, and allows a greater diversity of applications that we can service.
Principles of EBW
The process uses kinetic energy of electrons to produce heat. This heat can be used, for example, to weld 2 plates together.
As the beam of electrons strikes the joint between 2 components, the heat energy is sufficient to locally fuse two metal parts together, thus forming the weld joint.
The high speed electrons beam is tightly focussed, using magnetic fields, on the joint area between the parts. Typically the beam spot is about 0.2 mm in diameter.
EBW is performed in a vacuum, necessary to maintain beam focus. There are no impurities left by the process, and oxides and nitrides are eliminated. Any other impurities are vaporised.
Being a vacuum process, and using high voltages, the process is automated, using a computer control system. Often specialised fixtures are used inside the chamber, for location and manipulation of workpieces. Usually these are made from non-magnetic materials, to avoid any distortion of the focussing of the electron beam.
Factors Governing EBW Applications
- Weld penetration is controlled by adjustment of electron beam output power. Therefore, EBW is applicable to a wide variety of base materials, from thin to thick sheets.
- Metals having high melting points, for example Tungsten and Niobium, are particularly suitable for EBW process.
- It can be used for active metals like Titanium, which may oxidise during conventional welding.
- Joints which use refractory materials, not weldable using conventional techniques, can be electron beam welded. This is also true for dissimilar metals.
- Because of focussed and localised heat input, shrinkage and distortion are mimimised.
- Welds up to 95% of the strength of base materials are obtained.
Industries using EBW Processes
- Aerospace & defence
- Energy
- Fuel cells
- Medical
- Sensors
- Semiconductors
- Oil & gas
- Automotive
- Fibre optics
- Microelectronics
- Microwave
- Fluid valves
- Marine
- Nuclear
EBW Process Advantages
- Welding of both similar and dissimilar materials, including refractory
- Low heat input gives minimal shrinkage or distortion of workpieces
- The surface finish obtained is high
- The heat effective zone, and weld area, is small
- Resultant welds are high strength, up to 95% of base materials strength
- Vacuum process minimises welding defects and impurities
- There is no requirement for filler or flux material
- Beam welding is very precise in weld positioning
- It provides a high metal joining rate
- Weld penetration of 0.05 mm to 50 mm is achievable
- Precise control of the automated process, gives high batch repeatability
- As above, the welding process is always fully automated
- Only process that can join high temperature metals, e.g. titanium & niobium
EBW Process Disadvantages
- Due to the small vacuum chamber, only small workpieces can be welded
- During welding, there is the issue of X-ray radiation that has to be treated
- The cost of the machinery required is very high
- The welding process involves skilled operators
- Because the EBW beam is tightly focussed, precise fits of parts are needed
- There is considerable and regular maintenance required
- The process is unsuitable for very thin metal sections
- For each production cycle, a vacuum has to be created in the chamber
Conclusions
Here at Davis Scientific Treatments, we are able to provide this Electron Beam Welding service.. As described above, there are many projects, where this operation is highly suitable as a workpiece jointing solution.
Please contact us, whether your project is a production one, or even if you are in R & D stage, looking for methods to move your project forwards. At least we will be able to give you some feedback on our capabilities, to maybe solve your particular problems.